He tenido el problema recurrente del testigo de desgaste de pastillas encendido en el tablero de instrumentos. Ya revise sensores, funcionan correctamente, cables ailsaldo (se corrigió el delantero) y funcionó por 3 semanas mas o menos. Como no me gusta la solución más simple que es quitar el bombillo del testigo, me encontré esta solución en RV3Unlimited.
Perdonen que esta en inglés, pero en resumidas cuentas dice que si los sensores, las masas y el cableado esta ok el problema esta en la tarjeta del tablero de instrumentos. Simplemente hay que resoldar una de las resistencias del circuito.
Alguno lo ha probado?
First, the advice to reset the sensor by turning on the ignition key for 2-3 minutes is bogus. The e36 and later have computer controlled brake lining warning lights. The one in the e30 is simple electronics with no memory.
The system is easy to diagnose and fix if you have the right information. The usual failures are worn through wiring caused by incorrectly routed cables or missing clips, or a bad resistor on the instrument cluster.
Here is my write-up
Brake lining indicator light
Summary: The light is triggered either by the wire grounding (usually against the brake rotor as the sensor is partially worn away) or the wire breaking (usually as the sensor is further worn away). If the sensors are fine, re-flow the solder on the instrument cluster resistor.
Operation
Most e30s with four wheel disk brakes have a brake wear monitoring system. The system uses two replaceable sensors to monitor the front and rear brake pad wear. The sensors are mounted in a notch on the
outer edge of the inboard brake pad on the left front and right rear. As the pad wears, the sensor faces are ground away with the brake pad friction material.
The sensors are simply a wire embedded in an insulating material. The brake wear circuit is similar to alarm system wiring: the indicator light illuminates when the sensor wire is either grounded or is broken.
When a sensor face first starts to wear against the rotor, the wire is initially exposed and grounds against the rotor only when braking. Later the wire is worn through, breaking the circuit. Thus the lamp is
initially illuminated only when braking, and later stays illuminated.
The sensor circuit is fed +12V through a 220 ohm resistor on the instrument cluster circuit board, through the right rear sensor, then through the left front sensor, then back to the circuit on the cluster.
If the wear indicator circuit doesn't work and the sensors are fine, the most common source of problems is the 220 ohm resistor. This can be easily tested without taking apart the instrument cluster. Turn on the
ignition to power the circuit and illuminate the wear indicator. Measure the voltage and available current on the right rear sensor connector. One of the contacts should read +12V, and provide 55-65 mA
to ground. The contact is the blue/white wire, not the green/yellow, but it's trivial to probe both rather than look for the wire color. Use the brake rotor as a clean ground.
If you aren't getting voltage or the correct current, the problem is very likely on the cluster circuit board. Remove the board and re-flow the solder around the 220 ohm resistor. This resistor is mounted next
to the C1 blue connector on the PC board. It sticks off of the board on long leads. There are on-line pictures to locate the resistor, and you can confirm the correct part by looking for the red-red-brown color bands.
This might sound daunting if you haven't soldered before, but this is the easiest soldering task ever. Let the soldering iron warm up for a few minutes, then touch the soldering iron tip to each resistor lead for two
to five seconds. You should see the solder surface change texture as it melts, filling in the cracks that have grown over time.
Add a dab of silicone to mechanically support the resistor so that the solder doesn't crack again. Don't cover the resistor, as it has to dissipate almost 1 watt of heat if the sensor wire is touching ground.
That heat is likely why the resistor is mounted so far off the board to start with -- the designers didn't want to use a expensive 1.25W resistor, when a common 1/4W resistor was adequate most of the time.
But they didn't consider that worn-through sensors and holding the brakes on for an extended period (e.g. stop-and-go traffic) are correlated. The resistor is at 4X its power rating, and the only place
for the heat to dissipate is through the resistor leads. Now you have the mechanical leverage from mounting the resistor far from the board "working" the solder combined with thermal expansion cycles from the
overheating. No wonder there is cracking!
Worst-case power analysis for the 220ohm sensor supply resistor.
220ohm, 10% tolerance = 198-ohms, 5% tolerance = 209-ohms
Nominal 12V power is typical 13.8V operating, 15V hot load.
Power = V*I = V*V/R
Worst-case 15V*15V/198ohms = 1.14W
Worst-case, 5% 14.4V*14.4V/209ohms = 1.00W
Typical/nominal 13.8*13.8/220 = 0.87W
Design safety worst case 18V*18V/198ohms = 1.64W
So the designer should have specified at least a 1.25W part.
Note: I previously assumed that the lamp check was done by providing the sensor power through the unloader relay. That would test the lamp drive circuitry as well as the lamp. Instead the lamp check is done with a diode isolated feed from the start circuit.
While you have the cluster out, with soldering iron at hand, re-flow the solder around the temperature meter mounting hole. One of the contacts is through the sleeve around the brass mounting stud. The stud pulls
the sleeve into the soft solder on circuit board to make contact. Over time the solder deforms, resulting in bad contact. Tightening the mounting nut will help for a bit, but building up the solder is a longer
term fix. Better, solder on a thin brass washer.
Perdonen que esta en inglés, pero en resumidas cuentas dice que si los sensores, las masas y el cableado esta ok el problema esta en la tarjeta del tablero de instrumentos. Simplemente hay que resoldar una de las resistencias del circuito.
Alguno lo ha probado?
First, the advice to reset the sensor by turning on the ignition key for 2-3 minutes is bogus. The e36 and later have computer controlled brake lining warning lights. The one in the e30 is simple electronics with no memory.
The system is easy to diagnose and fix if you have the right information. The usual failures are worn through wiring caused by incorrectly routed cables or missing clips, or a bad resistor on the instrument cluster.
Here is my write-up
Brake lining indicator light
Summary: The light is triggered either by the wire grounding (usually against the brake rotor as the sensor is partially worn away) or the wire breaking (usually as the sensor is further worn away). If the sensors are fine, re-flow the solder on the instrument cluster resistor.
Operation
Most e30s with four wheel disk brakes have a brake wear monitoring system. The system uses two replaceable sensors to monitor the front and rear brake pad wear. The sensors are mounted in a notch on the
outer edge of the inboard brake pad on the left front and right rear. As the pad wears, the sensor faces are ground away with the brake pad friction material.
The sensors are simply a wire embedded in an insulating material. The brake wear circuit is similar to alarm system wiring: the indicator light illuminates when the sensor wire is either grounded or is broken.
When a sensor face first starts to wear against the rotor, the wire is initially exposed and grounds against the rotor only when braking. Later the wire is worn through, breaking the circuit. Thus the lamp is
initially illuminated only when braking, and later stays illuminated.
The sensor circuit is fed +12V through a 220 ohm resistor on the instrument cluster circuit board, through the right rear sensor, then through the left front sensor, then back to the circuit on the cluster.
If the wear indicator circuit doesn't work and the sensors are fine, the most common source of problems is the 220 ohm resistor. This can be easily tested without taking apart the instrument cluster. Turn on the
ignition to power the circuit and illuminate the wear indicator. Measure the voltage and available current on the right rear sensor connector. One of the contacts should read +12V, and provide 55-65 mA
to ground. The contact is the blue/white wire, not the green/yellow, but it's trivial to probe both rather than look for the wire color. Use the brake rotor as a clean ground.
If you aren't getting voltage or the correct current, the problem is very likely on the cluster circuit board. Remove the board and re-flow the solder around the 220 ohm resistor. This resistor is mounted next
to the C1 blue connector on the PC board. It sticks off of the board on long leads. There are on-line pictures to locate the resistor, and you can confirm the correct part by looking for the red-red-brown color bands.
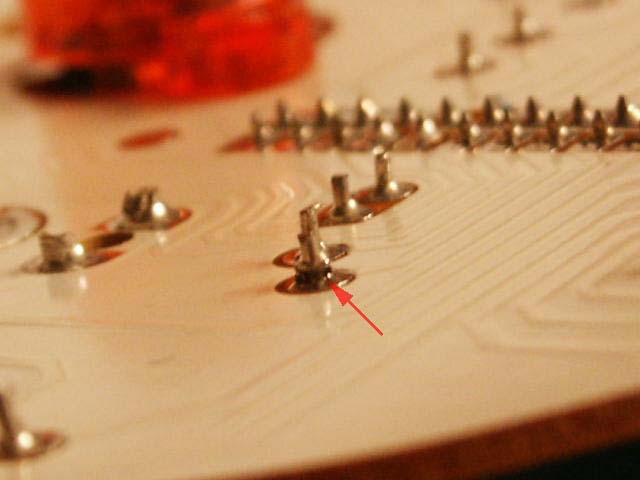
This might sound daunting if you haven't soldered before, but this is the easiest soldering task ever. Let the soldering iron warm up for a few minutes, then touch the soldering iron tip to each resistor lead for two
to five seconds. You should see the solder surface change texture as it melts, filling in the cracks that have grown over time.
Add a dab of silicone to mechanically support the resistor so that the solder doesn't crack again. Don't cover the resistor, as it has to dissipate almost 1 watt of heat if the sensor wire is touching ground.
That heat is likely why the resistor is mounted so far off the board to start with -- the designers didn't want to use a expensive 1.25W resistor, when a common 1/4W resistor was adequate most of the time.
But they didn't consider that worn-through sensors and holding the brakes on for an extended period (e.g. stop-and-go traffic) are correlated. The resistor is at 4X its power rating, and the only place
for the heat to dissipate is through the resistor leads. Now you have the mechanical leverage from mounting the resistor far from the board "working" the solder combined with thermal expansion cycles from the
overheating. No wonder there is cracking!
Worst-case power analysis for the 220ohm sensor supply resistor.
220ohm, 10% tolerance = 198-ohms, 5% tolerance = 209-ohms
Nominal 12V power is typical 13.8V operating, 15V hot load.
Power = V*I = V*V/R
Worst-case 15V*15V/198ohms = 1.14W
Worst-case, 5% 14.4V*14.4V/209ohms = 1.00W
Typical/nominal 13.8*13.8/220 = 0.87W
Design safety worst case 18V*18V/198ohms = 1.64W
So the designer should have specified at least a 1.25W part.
Note: I previously assumed that the lamp check was done by providing the sensor power through the unloader relay. That would test the lamp drive circuitry as well as the lamp. Instead the lamp check is done with a diode isolated feed from the start circuit.
While you have the cluster out, with soldering iron at hand, re-flow the solder around the temperature meter mounting hole. One of the contacts is through the sleeve around the brass mounting stud. The stud pulls
the sleeve into the soft solder on circuit board to make contact. Over time the solder deforms, resulting in bad contact. Tightening the mounting nut will help for a bit, but building up the solder is a longer
term fix. Better, solder on a thin brass washer.
Última edición por un moderador: